SWAN Corner Forming Machine For Traffic Road Signs
corner forming Rectangular&triangle&octagonal shape, corner moulding machine, R52 raduis maximum cornerformer
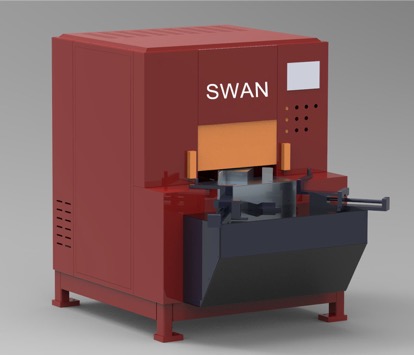
SWAN Corner Forming Machine For Traffic Road Signs forming prefect corners, No longer needed welding, NO set up. NO welding. NO grinding. NO finishing. NO polishing.
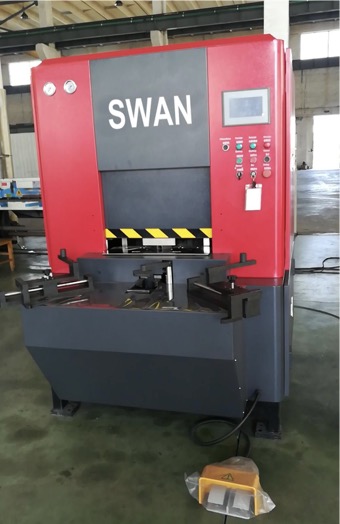
SWAN Corner Forming Machine For Traffic Road Signs forming prefect corners, No longer needed welding, NO set up. NO welding. NO grinding. NO finishing. NO polishing.
The forming and shearing is finished separately in two working Position, Install safety light curtain protection to make the production process more safe and humanistic, The accuracy of different thickness is controlled by Fuji servo motors, Parameters is adjusted through touch screen, some other movement is controlled by Mitsubishi PLC.A set of mould is with the machine ,including roller tool ,square tool ,shear cutter of a corner radius.
Adopt the imported first-class brand components as our key electrical components to ensure the reliability and stability of the system.
The PLC controller with 68 points can store and save lots of sheet metal corner moulding technologies, gap compensation coefficients .At the same time ,it can save and rewrite the coefficients of special materials and even the complex bimetal at any time This machine improves work efficiency more than three times by changing the tedious process of open-angle welding ,grinding etc into rolling,stretching and forming directly .it saves labor ,electricity ,gas , grinding material and other accessories for enterprises, therefore ,it is both environmentally friendly and greatly reduces the production cost , could be regarded as the enterprise save-money expert.
There are only 2 step to forming the corner:
Step1: Bending the 4side flange by special bending tools
Step 2: corner former by Corner Forming Machine
Final lay-out products:
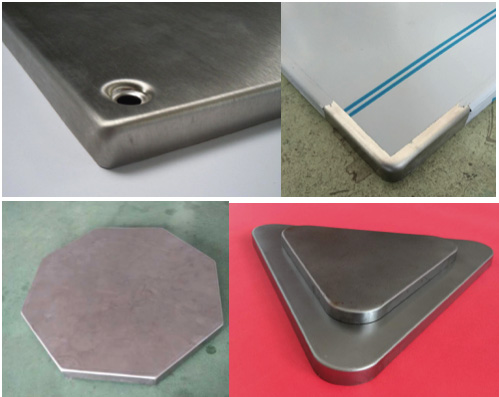
PRODUCT PROFILES:
corner Forming DieR CO
The flexible corner former for panel and door fabrication allows you to create high quality corners up to 10x faster than welding, which reduces cost.
A new flexible state of the art technology known as: FLEXIBLE Corner Forming Machine
gives new opportunities in metal sheet production of panels or doors. Cold forming of corners on doors or panels in any material formable (Mild Steel, Stainless Steel, Aluminium, alloys and others) allow to use any material thickness and individual flange heights
Corner Forming Machine COST & TIME SAVINGS:
Cost Saving:no welding, no hand finishing work; only 1 operator required; elimination of abrasives and welding consumables;
Comparison of Traditional Processing Technology and Corner Forming Process:
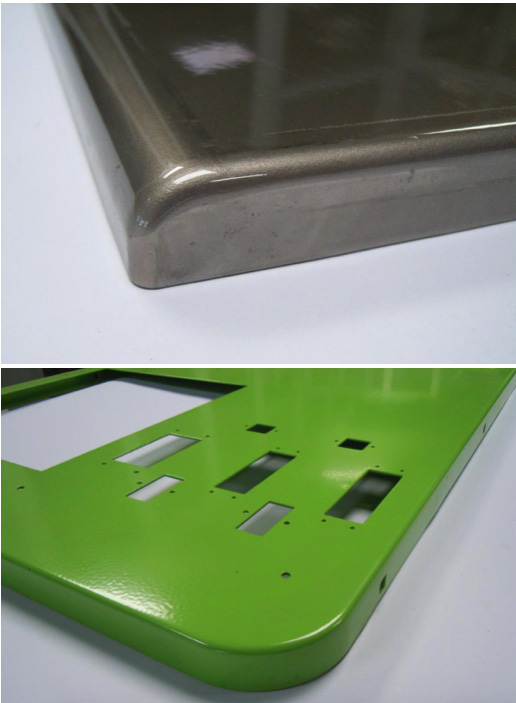